The front module technology was developed for Model S II and Model X II, which initially were only sold in the USA. The objective was to reduce the number of components, reduce weight and to push technology boundaries.
Tesla were not alone in pursuing this goal. BMW for example had worked on this technology nearly three decades ago, but while components could be engineered to produce variable yield throughout the part – progressive deformation from the extremities to the front wheel centreline – process consistency was a real issue. Some castings would not behave as intended.
Further, Porsche on the 981 Boxster / Cayman and 991 ‘911’ had significant front and rear aluminium alloy sub-modules joined to a steel and aluminium alloy intensive central structure, allowing the entire removal of each module or localised repair depending on the extent of the damage.
Tesla do not permit use of pulling on the body structures due to the number of bonded joints.
Tesla Cybertruck – not destined for Europe at the moment since it does not conform to elements of EU25 plus UK whole vehicle type approval – takes the large ideas we have seen so far and, well, expands them. Aside from the stainless-steel skin panels, door and tailgate structures, there are two simply enormous die castings. The front module has the next generation of ‘freeform’ webs, allowing the aluminium alloy to flow into position more easily before crystalline formation. The same design process was used for the rear module as well.
Ever bigger die casting machines and selective zone cooled tools mean it is not possible to deviate from the manufacturer’s repair process.
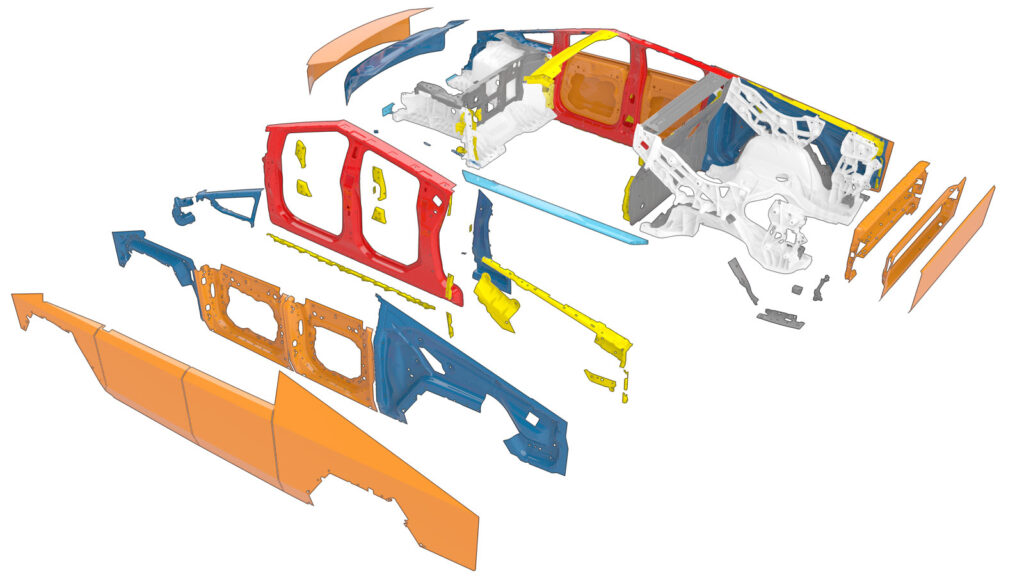