The first phase of large-scale aluminium alloy pressure die casting for the body structure at Tesla was a rear module which integrated the rear chassis legs, two cross members and the inner rear wheel arches. Note the forward tabs with connect to the steel sill panels, and the sacrificial aluminium alloy members between the rear bumper beam and the ‘mega casting’.
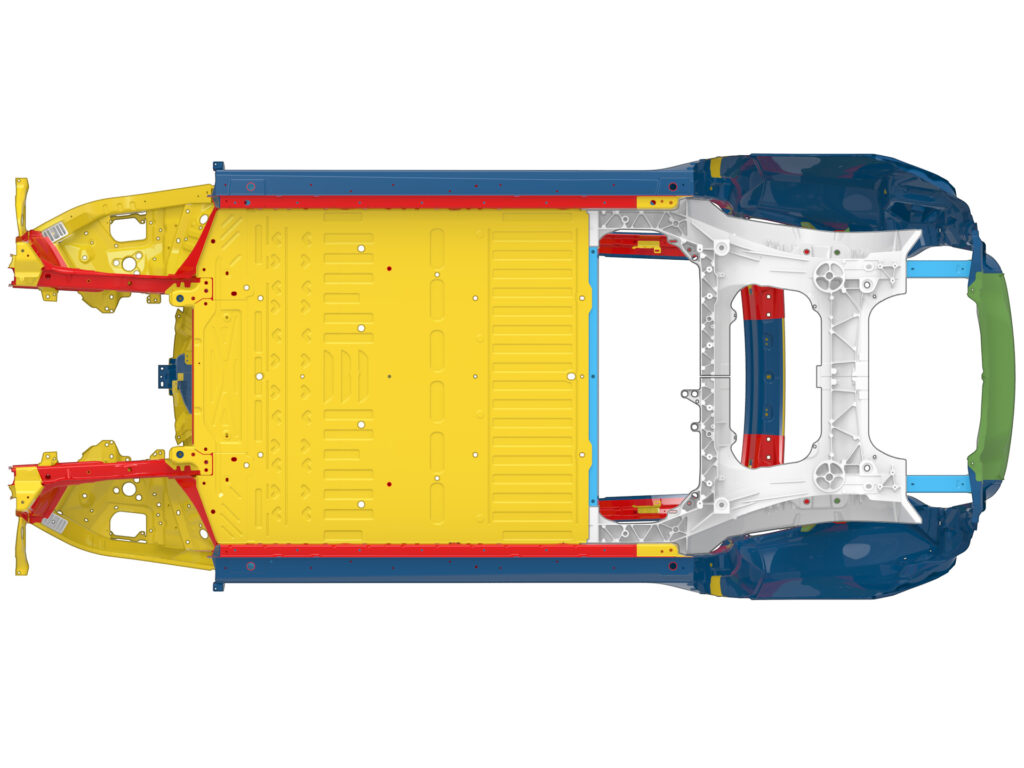
This replaced a mix of pressings and castings premiered on Model 3, to reduce assembly time as well as to provide a small weight saving. The component was made as a single- or two-piece assembly, with appropriate collision repair instructions for each solution.
In effect the material flow during the casting process had to produce the correct crystalline structure – hence the immense pressure to ensure molten metal flowed throughout the mould before cooling – but did not require progressive yield beyond the basic mechanical structural demands.
The next step was piloted at the Tesla assembly plant in Austin, Texas. Learning from the engineering to create the first rear module, the team worked with the supplier to develop castings with variable heat treatment which allowed integration of the rear chassis leg sacrificial elements as well as the forward cross member:
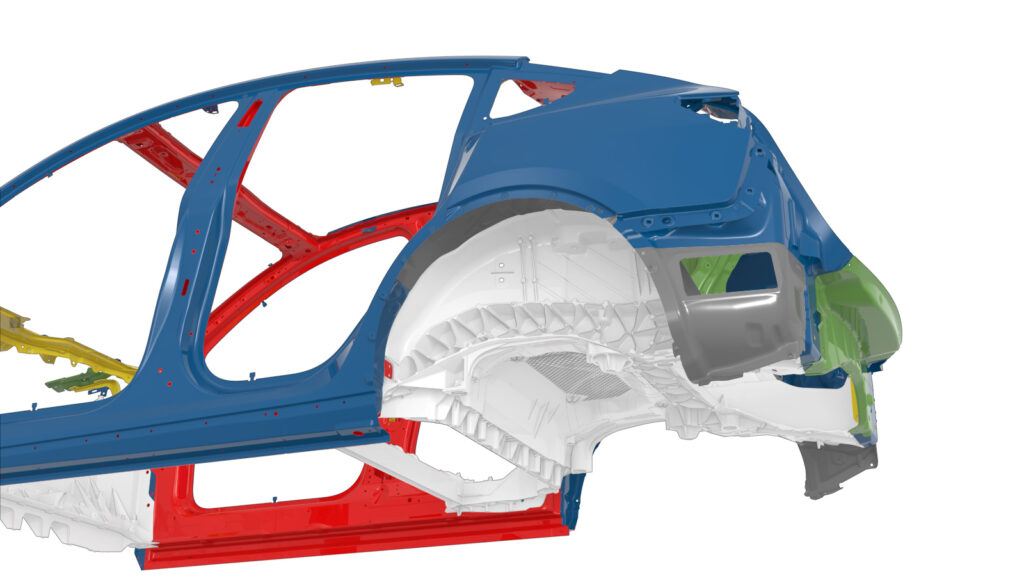
Well, to achieve this on the rear end would be ambitious, but to do so on the front….
But we’re not done yet. The upper face of the battery pack was fitted with the interior carpet, centre console and front seats, to be fitted as an assembled module into the body structure.
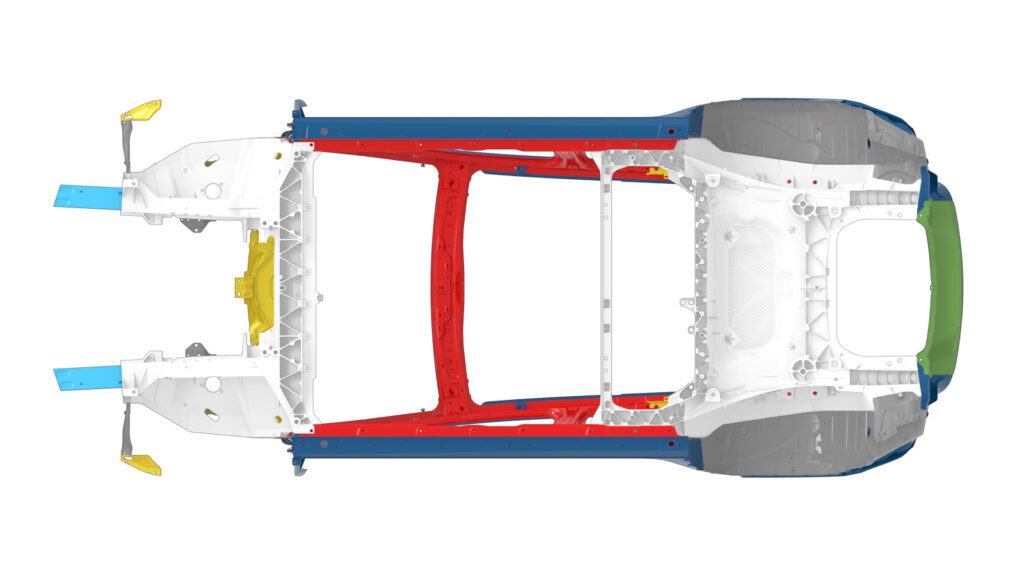