VWG had a painful development of group-wide and product-wide software via the internal division Cariad, leading to the loss of several company leaders and product introduction delays. To help out, an intermediate package called E3 1.2 (‘End to End Electrical’ architecture V1.2)– which reduces the entire vehicle control system to 5 main high-performance computers (‘HCP’) modules, which cover the entire vehicle electronic system functions.
The next part was the first dedicated BEV platform for mass-market Audi – the Premium Platform Electric (‘PPE’). There is also a Premium Platform Combustion (‘PPC’) for internal combustion engine powered versions – yes, that’s the ICE.
Audi Q6 e-tron has an aluminium bonnet, tailgate, bumper beam assemblies, front chassis leg, front strut tower casting as well as one of the two sill reinforcement members. The parts shown in purple are all hot formed UUS steel – the main floor, A pillar reinforcement, cant rail reinforcement, sill reinforcement (the second one), sill inner, and rear chassis leg. The flat main floor in hot formed UHS steel alloy is a new feature for VWG – it has transverse members to transfer impact energy across the car in the event of side impact.
The battery has internal structural members running parallel to the longitudinal axis of the car, which are attached to the floor with 10 screws – this is different. The battery, when removed, requires the fibre reinforced undershield to be unscrewed from the body, then a few major screws from the underside followed by the 10 screws from inside the passenger compartment. The 10 screws can be accessed via covers and flaps in the interior carpet, without removal of the front seats or centre console. The battery pack is then lowered with the undershield attached to it.
The traction battery is liquid cooled and can be charged via one port at 800V or both the left-hand and right-hand charge ports at 400V (parallel charging). The 100 kWh Li-Ion battery pack has 12 modules, each containing 15 cells prismatic cells made by CATL – the nominal voltage is 672V and the weight around 590 kg. There is an 83 kWh version of the Li-Ion battery for rear wheel drive models with 10 modules, again each with 15 prismatic CATL cells in each module.
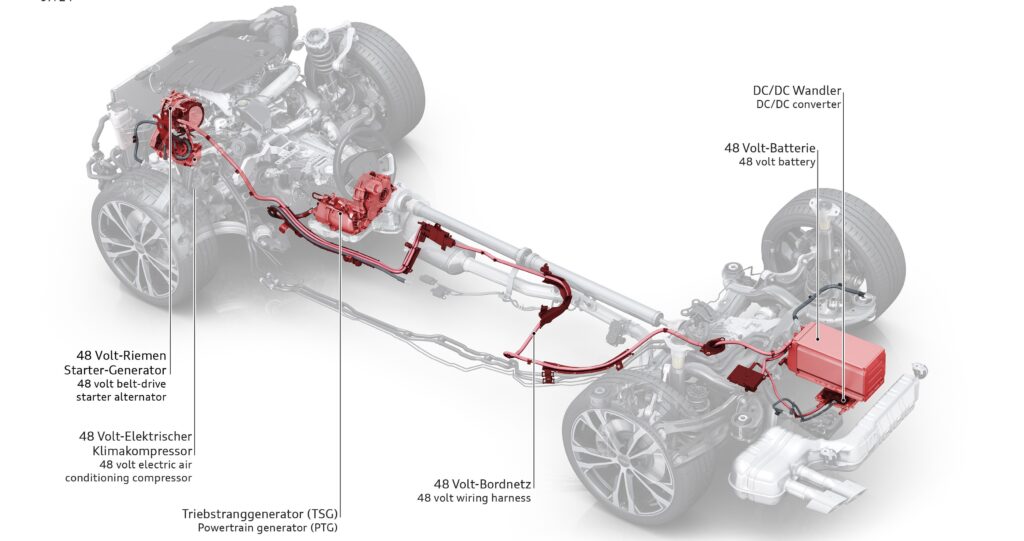
The platform is available with four-wheel drive or rear wheel drive – the power and torque variations refer to peak outputs available for up to 10 seconds at a time. In the event of impact, the high voltage system (power electronics, motors, inverter, battery, charger, charge ports) is isolated in 2 seconds.
Each motor module features self-contained oil cooling, with an oil to water-glycol coolant heat exchanger. The battery uses a water-glycol heat exchanger on the lower face of the battery pack, which is connected to the standard fitment heat pump in the AC circuit (with R1234yf rather than R744 refrigerant) as well as the radiator. Each of the modules sends state of charge and thermal information to the High Performance Computer (‘HPC’) No5. There are two electric heaters – one for the interior inside the dash panel and one for the battery to warm it up if required, located on the upper cover. Overall, the thermal system is typical of a BEV – each system has to be maintained within a specific temperature range, which could require cooling or heating. The side view of the package emphasises the battery pack position at the lowest point of the vehicle.